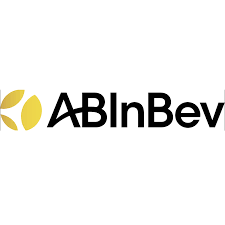
MRP Specialist at AB InBev Tanzania
Job Role Insights
-
Date posted
2025-05-16
-
Closing date
2025-05-24
-
Hiring location
Dar es Salaam
-
Career level
Middle
-
Qualification
Bachelor Degree
-
Experience
2 Years 3 Years
-
Quantity
1 person
-
Gender
both
Job Description
The key purpose of this role is to connects every dot of the manufacturing supply chain from demand through to supply, logistics and finance. The purpose is to generate feasible monthly supply & inventory plans that meet desired customer service Levels while avoiding unnecessary distribution and obsolescence costs.
Key Roles and Responsibilities:
- Ensure an updated 13-week plan linked to WSNP publish is produced and shared to mitigate short term risks.
- Monitor the weekly plans produced by the SNP team and escalate risks to MRP Manager and SNP manager.
- Produce a monthly 12-18 month raw materials forecast aligned to S&OP and CONA. Publish & Sign off on monthly inventory LE’s,
- Support operational MRP to the breweries and in BSC structure – linking short term plans with Exec S&OP,
- Oversee tactical raw material as part of the S&OP process. Own and drive Inventory Policy, published as per requirements,
- Ensure monthly ‘handshake’ on S&OP process with suppliers and procurement, and routines are followed,
- Actively working with the portfolio and marketing teams on any promotions, write off risks and changes in packaging,
- Support cash flow routines on materials and work on materials Core Working Capital latest estimates.
- Control/Loss prevention and Obsolete Management
- Protect service level by identifying and mitigating risks on raw materials
- KPI tracking: Materials Out of Range, DCBL Materials, Materials DIO, NST, OTIF Materials, S&OP KPI’s on supplier collaboration
- LCP owner of Material and Inventory Pillar/Blocks.
MRP Run & Validation
- Run MRP in the Planning System for both TBL and TDL &Check restrictions and adjust. Ensure effective use of Barton Planning System
- Check material availability and forward stock projection vs agreed upon stock parameters for both TBL and TDL
- Review supplier production plan and critical material availability, check restrictions and adjust
- Identify slow moving inventory and alert team
- Check long term material availability with suppliers
Material Management
- Expediting of urgent orders & Ensure correct PO process is followed
- Follow up that all inventory is GRN in time (within 48 hours) and that GIT is always clean
- Carefully track and report on shelf life of materials weekly and monthly to reduce obsolescence risk
- Manage inventory levels against Inventory Policy and report weekly on any variances and risks
- Ensure ONTIME system usage, adoption and adherence – track KPI’s
Supplier Management
- Fully understand commercial terms of each supplier & Issue POs for each raw material and packaging materials at brewery and distillery level
- Follow up with supplier monthly on any account related problems and facilitate speedy reconciliation of accounts.
- Manage call offs from suppliers
Cost management
- Manage materials within cash flow budgets & Identify and implement cost avoidance and cost reduction initiatives
Master data management
- Regularly reviewing all master data with various functions in the organization as well as suppliers to ensure data quality and accuracy
- Drive regular routines to keep master data up to date in the planning tool. This includes but are not to inventory on hand and order lead times, BOM, production schedule, minimum order quantity etc.
- Define critical materials and raw material risk matrix
KPI’s, Routines & Reports
- Ensures that Daily, Weekly and Monthly Meeting routines are adhered to in line with mandatory LCP & internal guidelines
- Ensures that processes are standardized via SOP's and work standards are monitored and improved by using Operational Work Diagnoses (OWD’s);
- Track KPI's on a daily, weekly and monthly basis in line with LCP requirements
- Ensures that appropriate problem-solving tools are applied for out-of-range KPI's in line with LCP methodology.
- Publish reports on time as per LCP guidelines and internal processes.
Key Attributes and Competencies:
- Effective numeracy and analytical skills & problem solving at both operational and tactical levels
- Ability to manage complexity and ambiguity
- Good communicator across all levels within and external to the organization
- Strong negotiation skills and ability to build rapport and influence across all levels in the organization
- Excellent self-management practices with a pro-active, energetic and committed approach
- Excellent presentation and report drafting skills
- Excellent analytical understanding and strong excel capabilities advantageous
- Ability to manage multiple streams of information optimally with attention to detail
- An orientation towards the quantitative disciplines of mathematics, statistics and economics would be advantageous
Minimum Requirements:
- Candidate should have a 3-year Bachelor level degree in Sciences, Supply chain, Commercial or similar degree or equivalent tertiary education
- 2-3 years planning experience advantageous
Interested in this job?
7 days left to apply
Share this opportunity
Help others find their dream job